Processi sottovuoto alla giusta velocità
Fino ad oggi le unità di trattamento al plasma a bassa pressione sono state il collo di bottiglia sulle linee di produzione. Ora attraverso la combinazione di un sistema di trattamento al plasma a ciclo breve con un sistema di trasporto disaccoppiato, la fase di attivazione può essere ben integrata nelle linee di produzione.
Le fasi di produzione che richiedono la movimentazione manuale delle parti sono costose e possono essere integrate solo in misura limitata nei processi di produzione e assemblaggio interconnessi tra loro. Le aziende che utilizzano sistemi automatizzati per il trasporto dei pezzi cercano di automatizzare tutte le fasi di movimentazione necessarie.
Se, ad esempio, lo stampaggio di un pezzo in termoplastica è direttamente seguito dal processo di finitura o di incollaggio, per i materiali non polari è necessaria una fase di attivazione. Ciò aumenta l’energia superficiale e garantisce la forza adesiva dello strato di rivestimento. Se il componente ha una geometria complessa o si trova in un sistema per il trasporto automatico dei pezzi, è necessario utilizzare un processo sottovuoto per poter agire sull’intera superficie del pezzo.
I processi al plasma a bassa pressione sono spesso ancora associati all’assemblaggio manuale e a lunghi tempi ciclo e quindi non sono presi in considerazione per applicazioni in linea. Le unità Plasma Technology sono state ottimizzate per permettere un’attivazione mediante plasma compatibile con il ritmo delle linee automatizzate, in modo che il tempo ciclo del trattamento non sia più la variabile che condiziona la velocità delle stesse.
Attivare le parti in 30 secondi
Plasma Technology, rende possibile realizzare un trattamento sottovuoto in linea con gli altri processi utilizzando un sistema di trasporto disaccoppiato per eseguire l’attivazione mediante plasma sul pezzo senza spostarlo dal sistema di trasporto che lo movimenta lungo la linea produttiva. Poiché l’elemento della linea che supporta il pezzo costituisce la parte inferiore della camera sottovuoto, esso viene modificato strutturalmente per poter garantire la tenuta del vuoto.
L’implementazione viene adattata individualmente al processo di produzione. Il pezzo, oppure l’assieme di parti da trattare, viene trasferito attraverso il sistema di trasporto della linea o altro dispositivo di movimentazione all’impianto di trattamento plasma. A quel punto un’apposita cappa discende sul supporto e crea la camera del vuoto. Appena la cappa ed il supporto del pezzo entrano in contatto inizia il processo. Il volume della camera e la pompa del vuoto sono dimensionati in modo che l’intero ciclo (evacuazione dell’aria, attivazione al plasma, ripristino della pressione, apertura) venga completato in 20-30 secondi. Ora il supporto può trasferire il pezzo alla stazione successiva della linea di produzione.
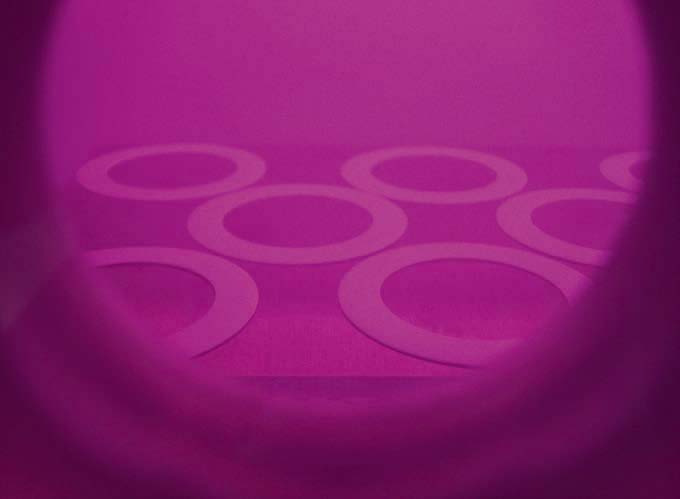
Movimentazione senza contaminazione
Ad esempio, è attualmente in fase di implementazione la seguente sequenza: il robot estrattore di una pressa per stampaggio a iniezione rimuove ogni pezzo e lo posiziona su un apposito supporto. Il sistema di movimentazione sincronizza l’abbassamento della cappa in modo da formare la camera a vuoto e inizia il processo al plasma. Il pezzo attivato viene quindi poi trasferito alla posizione successiva. Qui viene preso in consegna dal robot a servizio degli impianti di verniciatura.
La rastrelliera dell’attrezzatura ora vuota viene abbassata e trasportata alla stazione di sollevamento al livello inferiore in modo che possa essere caricata nuovamente dopo essere stata sollevata. L’utilizzo di un processo di produzione così integrato garantisce che tutti i componenti passino attraverso la camera a vuoto e che nessun pezzo non trattato venga trasferito al reparto verniciatura. Inoltre, questo impedisce che impronte digitali o altri contaminanti entrino in contatto con la superficie del componente durante la movimentazione manuale dopo l’attivazione, compromettendo la perfetta adesione della vernice.
Indipendente da materiali e geometrie
Sono necessarie almeno tre informazioni per la pianificazione di un sistema von tempo ciclo breve:
- Velocità effettiva di linea
- Gamma dei pezzi da trattare
- Tipologia materiali da trattare
Sulla base di questi punti chiave e di un numero rappresentativo di test preliminari, vengono determinate le dimensioni della cappa al plasma e viene selezionata la relativa pompa del vuoto in modo da consentire tempi di pompaggio brevi. Poiché il sistema di trasferimento è disaccoppiato, in quest’area è possibile anche se necessario adeguare la dimensione del supporto dei pezzi, utilizzando dei supporti diversi da quelli presenti sul resto della linea.
La cappa costituisce il coperchio e le pareti laterali della camera sottovuoto, il supporto dei pezzi funge da base. L’area della base può essere ad esempio 600 × 800 mm, per l’integrazione con un sistema di verniciatura a letto piano. Ciò consente di introdurre un rack di verniciatura completo con un ciclo di attivazione e rivestimento a uno strato. L’altezza della cappa è sempre dimensionata sul componente più alto che viene introdotto nel sistema per l’attivazione. Il breve tempo di esposizione al plasma consente solo l’attivazione di superfici polimeriche pulite. Per la pulizia, la deposizione di strati o la strutturazione di superfici sono necessari tempi di processo dell’ordine dei minuti. Tali processi possono essere eseguiti anche con questo tipo di impianto.
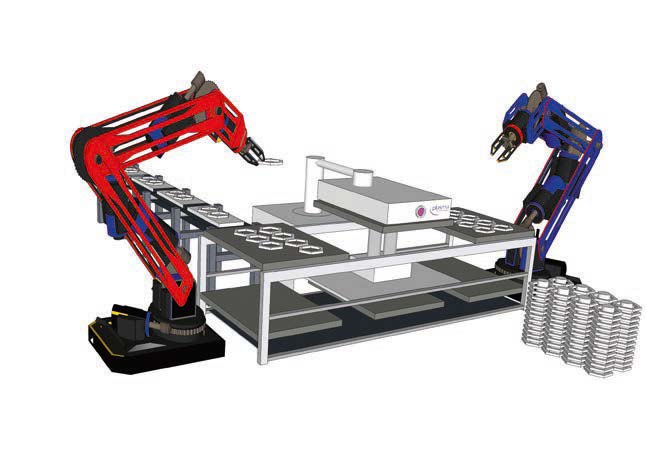
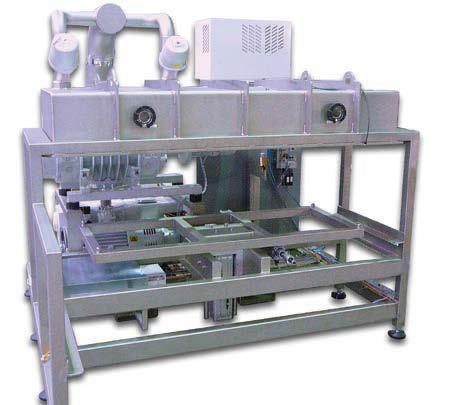
Dettagli tecnici di un sistema di riferimento
Volume camera: 200 litri
Volume utile = volume dei componenti: 120 litri
Ciclo di trattamento: 30 secondi
Volume / ora attivato: circa 14 m³
Volume attivato / 24 h: circa 350 m³
Potenza: circa 20 kW
Gas di processo: aria